Laser Welding in Oil & Gas Industry
Laser Welding Applications in the Oil and Gas Industry
In recent years, the oil and gas industry has increasingly adopted advanced welding technologies to enhance efficiency, safety, and reliability in operations. Among these technologies, laser welding has emerged as a transformative method due to its precision, speed, and ability to handle complex welding tasks. This article explores the applications of laser welding in the oil and gas sector, highlighting its benefits, challenges, and future prospects.
The Role of Laser Welding in the Oil and Gas Industry
Laser welding involves using a high-powered laser beam to melt and fuse materials, creating a robust and precise weld. This technology offers several advantages over traditional welding methods, particularly in the demanding environments of the oil and gas industry. Key applications of laser welding in this sector include:
Leveraging Cost-Effective and Qualified Welding Solutions for the Oil and Gas Industry
In the demanding realm of oil and gas welding and brazing, adherence to stringent standards is essential to ensure the integrity and reliability of all offshore equipment. Our services are designed to meet the highest qualifications in welding, as specified by industry standards such as ASME, DIN, and EN ISO 3834-3, and EN 729-2. These standards require meticulous attention to dimensional control and welding quality to withstand the harsh maritime environment, which is subject to rust, oxidation, wear, and other forms of deterioration.
Advanced Welding Capabilities
Utilizing welding equipment approved to DIN 14744, our operations are well-equipped to handle a variety of challenges including:
Comprehensive Testing and Qualification
To guarantee the quality and reliability of our welds, we conduct a range of rigorous tests, including:
By integrating these tests into our quality assurance protocols, we ensure that only high-quality, defect-free welds are completed, thereby upholding the highest standards of safety and reliability in the oil and gas industry.
Commitment to Quality and Cost-Effectiveness
Our commitment to leveraging qualified welding solutions is not only about meeting industry standards but also about providing cost-effective services without compromising quality. We understand the critical nature of welding in oil and gas operations and strive to offer solutions that deliver both performance and value.
By focusing on advanced technology and rigorous testing, we ensure that our welding services meet the highest standards of excellence while also being economically efficient. This approach enables us to support our customers effectively, providing them with reliable, high-quality welds that stand up to the harshest conditions.
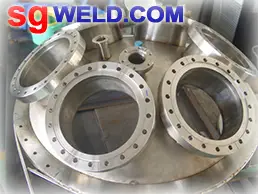
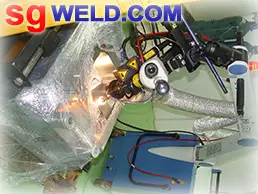

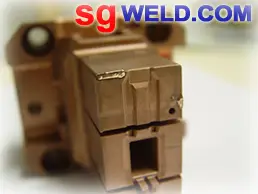
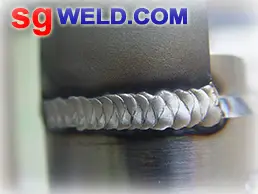
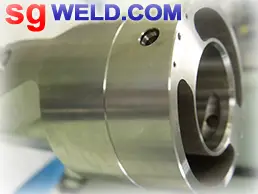
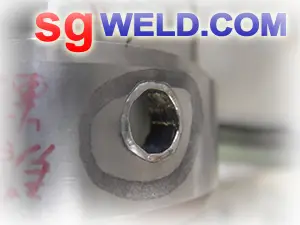


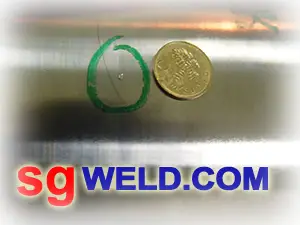
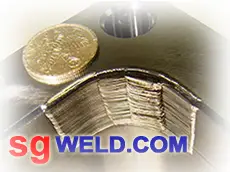
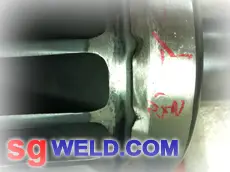
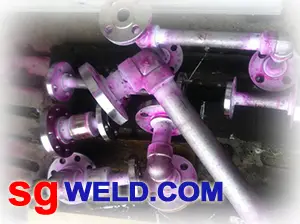
Laser welding has established itself as a crucial technology in the oil and gas industry, offering significant advantages in terms of precision, efficiency, and weld strength. While challenges remain, ongoing advancements and innovations are likely to address these issues and expand the technology’s applications. As the industry continues to evolve, laser welding will play a pivotal role in enhancing the reliability and performance of critical components and infrastructure.
By leveraging the benefits of laser welding, the oil and gas sector can achieve greater operational efficiency, safety, and sustainability, paving the way for future advancements in this vital industry.