Micro Laser Welding
Micro Laser Welding
Micro Laser Welding has emerged as a pivotal technology in precision manufacturing, revolutionizing how delicate components are joined with exceptional accuracy and efficiency. This advanced welding technique is increasingly adopted across various industries due to its unparalleled precision and the ability to handle intricate components. This article explores the fundamentals of micro laser welding, its significant advantages, diverse applications, and emerging trends shaping the future of this technology.
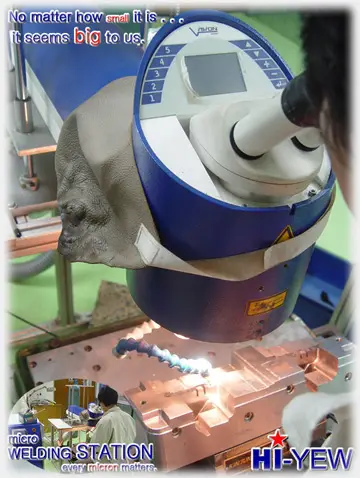
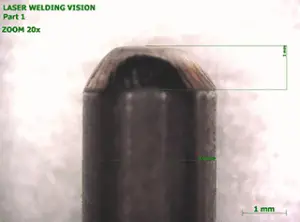
Principles of Micro Laser Welding
Micro Laser Welding leverages the focused energy of a laser beam to weld small-scale components with remarkable precision. This method differs from traditional welding techniques, which typically rely on electric arcs or flames to generate heat. Instead, micro laser welding uses a concentrated laser beam to deliver localized, intense heat, causing the materials to melt and fuse together. This technique is particularly beneficial for applications requiring high precision and minimal thermal impact on surrounding areas.
Applications of Micro Laser Welding
Micro laser welding is increasingly utilized across multiple industries due to its precise and efficient capabilities. Here are some prominent applications:
Electronics
In the electronics industry, micro laser welding is employed to join small and sensitive components such as connectors, leads, and circuit elements. The technology’s precision ensures reliable and durable connections while minimizing thermal damage to adjacent electronic components.
Medical Devices
The medical device industry benefits significantly from micro laser welding, particularly for joining delicate parts of devices such as implants, surgical instruments, and diagnostic equipment. The precision of laser welding ensures the integrity and functionality of these critical components, which often operate in stringent conditions.
Aerospace
Aerospace applications require highly reliable and precise welding of components subjected to extreme conditions. Micro laser welding is used to join parts in aircraft and spacecraft, including sensors, actuators, and structural components, where accuracy and strength are paramount.
Sensor Technology
The technology is also used for welding thermal elements, measuring sensors, and pressure membranes. Micro laser welding enables the placement of seam welds adjacent to temperature and vibration-sensitive electronic components, as well as welding in the membranes of pressure sensors, where precision and minimal heat impact are crucial.
Key Advantages
Precise Heat Application
Micro laser welding offers highly controlled heat application, with short-duration energy transfer that is localized and precise. This focused approach minimizes the heat-affected zone, reducing the risk of distortion and preserving the integrity of the components.
Narrow Seams
The technology ensures narrow seams with minimal angular distortion and transverse shrinkage. This precision is crucial for maintaining the structural and functional integrity of small components, particularly in applications where tight tolerances are required.
Economic Efficiency
Micro laser welding is a cost-effective technique due to its high welding speed and productivity. The ability to achieve precise welds without the need for additional filler materials or extensive post-weld processing contributes to reduced production costs. Furthermore, the technique supports alternative design options that can further minimize material wastage and overall expenses.
Material Optimization
One of the standout features of micro laser welding is its versatility with a wide range of materials. It accommodates various material types and combinations, allowing for optimization based on specific local requirements. This flexibility is particularly advantageous in industries that require the welding of dissimilar materials or complex geometries.
Advancements and Future Trends
Micro laser welding technology has advanced significantly over recent years, driven by increasing demand for higher quality and more reliable welds. Modern laser welding systems, such as those utilizing Nd(Neodymium-doped Yttrium Aluminum Garnet) lasers, offer enhanced performance and precision. These systems are compliant with stringent international standards, including ISO 9001:2000 and EN 46001 DIN – MED certifications, ensuring high quality and consistency in welding applications.
Technological Developments
Recent advancements in laser technology have introduced more sophisticated control systems and improved laser sources, resulting in enhanced welding capabilities. Innovations include higher power lasers with improved beam quality and advanced optics, which enable even finer control over the welding process. Additionally, integration with automated systems and robotics has further increased the efficiency and versatility of micro laser welding.
Future Prospects
Looking ahead, micro laser welding is poised to play a crucial role in the development of next-generation technologies. As industries continue to push the boundaries of miniaturization and complexity, the demand for precise and reliable welding solutions will grow. Emerging applications in fields such as nanotechnology, advanced electronics, and biocompatible materials are expected to drive further innovations in micro laser welding.
Micro Laser Welding represents a significant advancement in precision manufacturing, offering a range of benefits including precise heat application, narrow seam formation, economic efficiency, and material optimization. Its applications span diverse industries, from electronics and medical devices to aerospace and sensor technology. As technological advancements continue to enhance its capabilities, micro laser welding is set to remain at the forefront of welding technology, addressing the evolving needs of modern engineering and manufacturing.
For industries requiring meticulous and high-quality welding solutions, micro laser welding stands out as a powerful and versatile tool. Its ability to meet stringent specifications and deliver superior results makes it an indispensable technology in the modern manufacturing landscape.